Nous possédons tous des objets ou meubles « totem » pour lesquels nous vouons une affection particulière. Design élégant, présent de famille ou simplement marqueur d’un temps ou d’une époque révolue, ces objets n’occupent pas seulement l’espace, mais également nos souvenirs.
Seulement voilà, bien que le temps génère l’expérience, ses effets sont aussi nocifs sur les matériaux. Bois grisé ou cassé, plastiques ébréchés ou émiettés, telles sont des situations souvent rencontrées !
Il ne nous reste alors qu’à pleurer l’élégance déchue en invoquant le souvenir d’une image ou d’un parfum. Ou alors, se lancer dans l’aventure de la restauration. Evidemment, les pièces de remplacement ne se retrouvent pas dans un rayon de BricoMerlu. Il faut donc soit faire un bricolage sommaire, trouver un professionnel qualifié.
Le meuble de mémé, on l’aime mais pas au point de passer un SMIC dans sa réparation !
Pas de panique, en ce 21ème siècle, il faut vire avec son temps ! Aujourd’hui fabriquer sur mesure n’est plus une affaire de grimoires et d’outil dont on ne connaît pas les noms. Les technologies émergentes de fabrication numérique permettent de créer, dupliquer et donc de remplacer des pièces usagées ou cassées.
Les technologies numériques, c’est ce que l’on apprend au collège en fabricant un porte photo ?
Oui mais pas que ! Impression 3D / découpe laser / usinage CNC sont des composantes de cette révolution industrielle !
L’exemple que nous allons voir aujourd’hui est comment l’impression 3D peut-elle rénover des objets anciens.
Le début du projet
Tout commence par une photo. Nous recevons un e-mail d’un client qui cherche à restaurer une lampe de type « globe » sur pieds. Ayant cherché des moyens de réparation depuis quelques années, c’est l’âme en peine mais pleine d’espoir qu’il nous transmet une photo de l’objet en question et des réparations à effectuer.
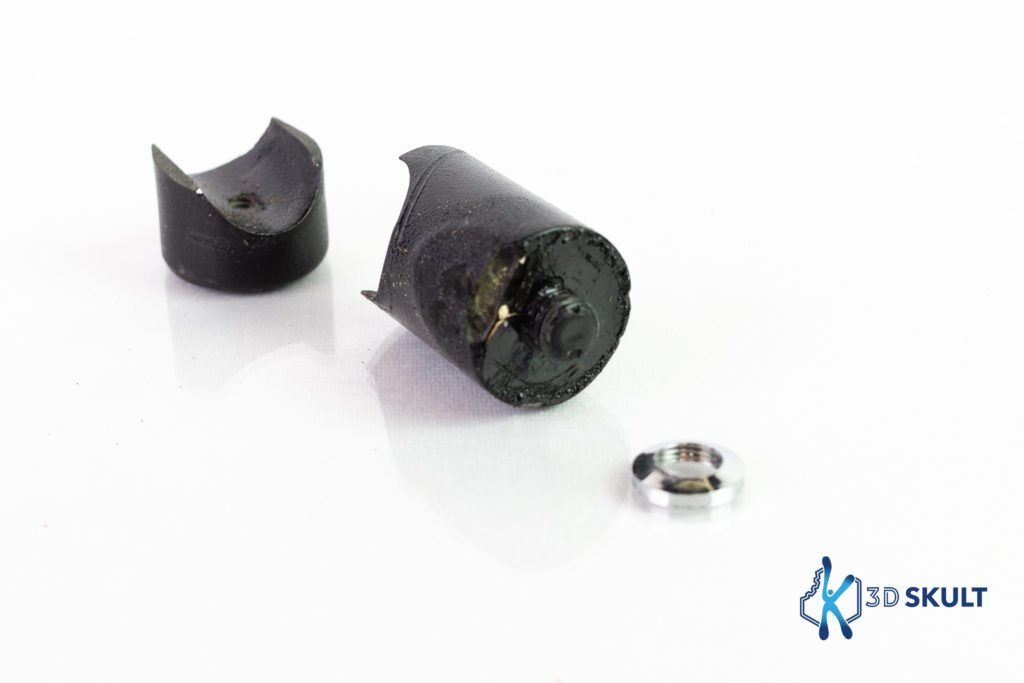
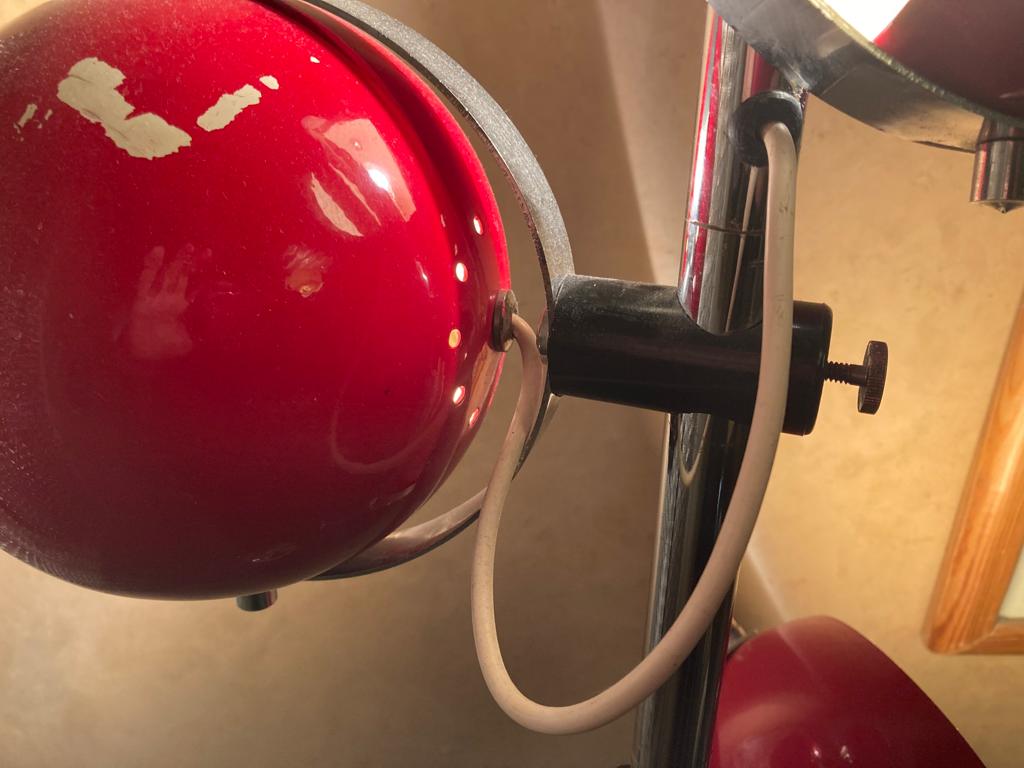
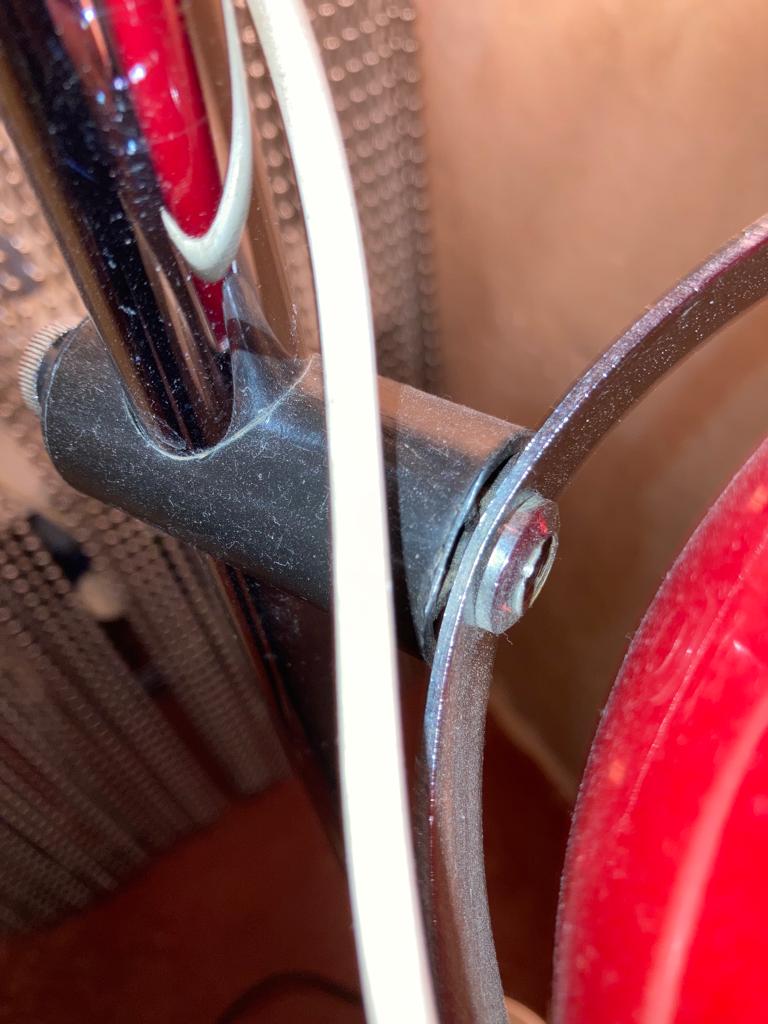
Une fois la pièce reçu, un diagnostic de casse est réalisé, doublé d’un relevé de côtes.
Détail du travail effectué
La pièce consiste en un cylindre, doté d’un alésage central permettant de coulisser le long d’un tube de structure. A une extrémité, un taraudage directement dans le plastique, permettant l’ajout d’une vis ayant pour but de maintenir le cylindre le long du tube de structure. A l’autre extrémité, un filetage plastique permettant de fixer une tôle pour la fixation du globe lumineux.
Plusieurs problèmes apparaissent sur cette pièce. En premier lieu, une rupture franche est survenue au milieu de l’alésage cylindrique. Le taraudage plastique est tellement usé que la vis de maintien n’est plus verrouillée lorsqu’elle est serrée. De l’autre côté, le filetage plastique est tordu et cassé, ne permettant pas non plus la fixation du support de globe.
Une seule pièce mais 3 problèmes !
Concernant la rupture de l’alésage cylindrique, la pièce a été modélisée en augmentant les parois (la toile) adjacentes d’une épaisseur de 1mm de chaque côté. Cela aura pour conséquence de renforcer cette zone et d’augmenter sa résistance.
Le taraudage plastique sera remplacé par adjonction d’un insert en laiton. Ainsi, le contact entre vis et taraudage sera métal/métal, augmentant drastiquement la durée de vie et la stabilité du système de maintien.
Enfin, le filetage servant à l’accueil de la fixation du globe sera remplacé par une tige filetée en inox, de diamètre 10 mm.
La quincaillerie ça compte aussi !
La vis de fixation au mât est remplacée par une vis avec embout cylindrique moleté, tout inox. Le diamètre supérieur couplé au moletage amélioreront grandement l’ergonomie pour le serrage.
Idem pour le filetage de 10 mm en inox qui se voit doté d’un nouvel écrou conique avec empreinte plate pour améliorer la fixation. Toujours en inox.
La pièce plastique cylindrique sera fabriquée par impression 3D en ABS. Le design revu augmentera également la rigidité de l’ensemble. Le taux de remplissage et l’épaisseur de paroi choisie renforceront le tout, de surcroît.
Le résultat
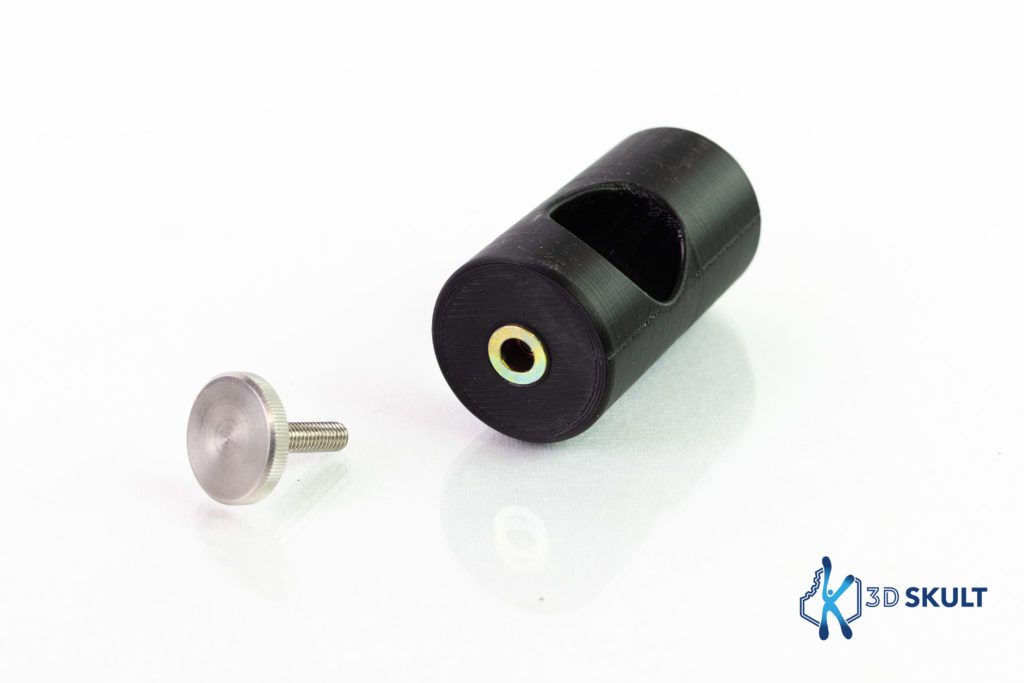
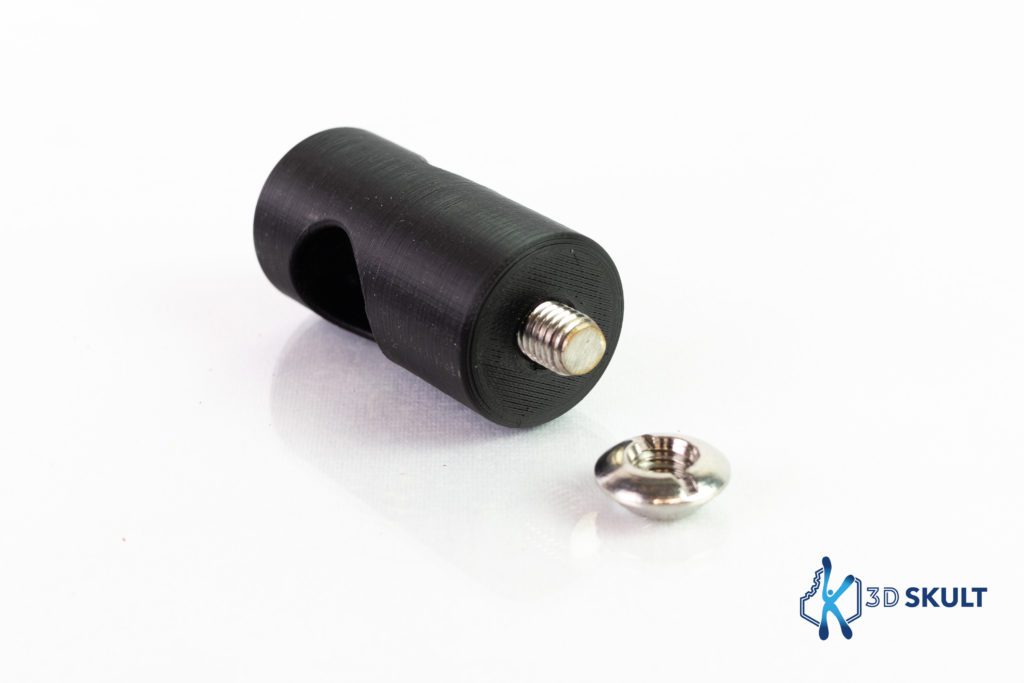
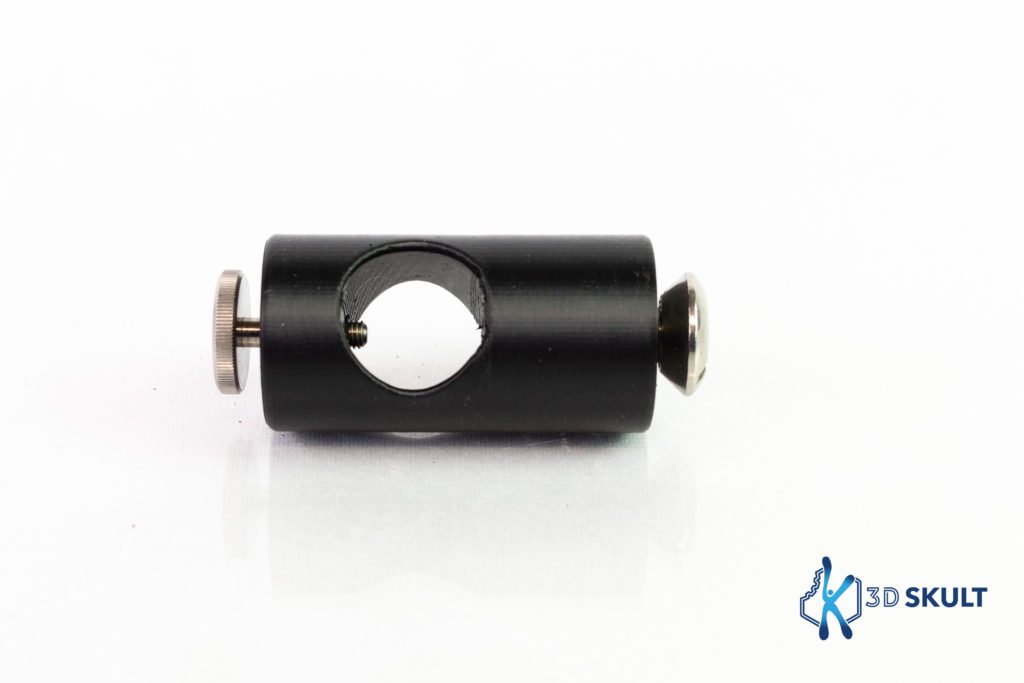
C’est ainsi que s’achève l’histoire de la rénovation de la lampe globe familiale qui vivra heureuse encore de nombreuses années. En bonus, nous n’avons pas fabriqué une seule mais 4 pièces au total, permettant le remplacement des 3 pièces existantes et une pièce de rechange !
Pour rappel vous retrouverez ci-dessous la photo avant/après du projet.
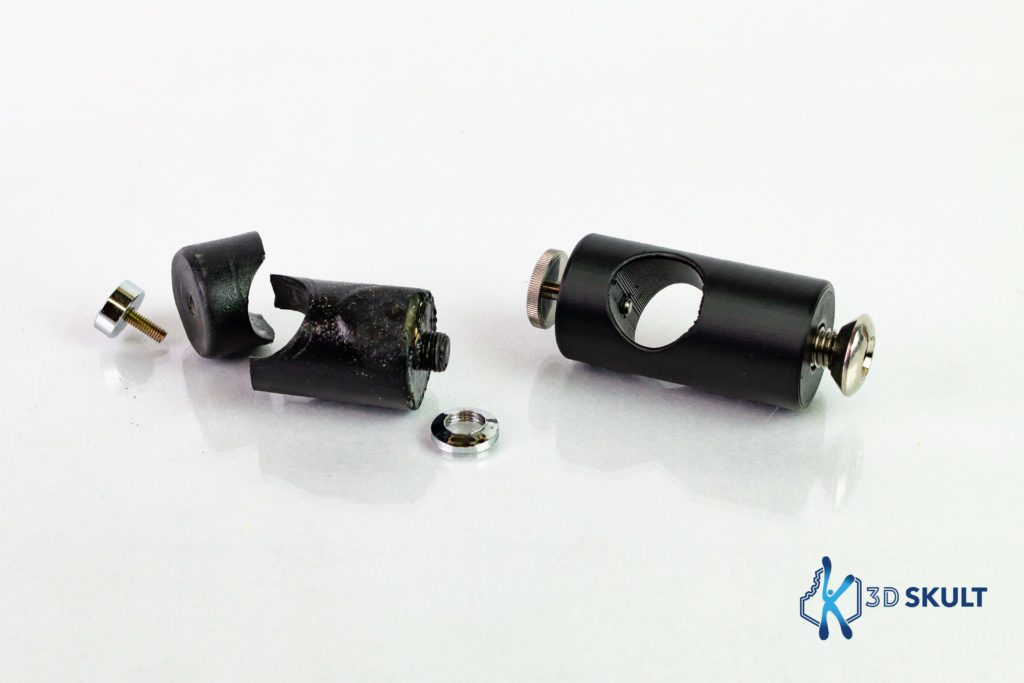