Lundi matin, 9h. En tant que responsable du parc machine de votre entreprise, vous faites le tour des différents ateliers afin de vous assurer que la semaine peut commencer en toute sérénité. Dans un élan de stupeur, vous constatez qu’une de vos machines a subi une casse au niveau d’un élément essentiel à la préservation de sa fonctionnalité. Ni une, ni deux, après avoir effectué un bref état des lieux, vous fouillez dans les dossiers de maintenance et recherchez les coordonnées du fabricant.
9h30, vous passez le coup de fil et une voix d’hôtesse vous annonce que le numéro que vous venez de composer n’est plus attribué.
Malgré l’accélération de votre rythme cardiaque et les quelques gouttes qui commencent à naître à la racine de votre front, vous décidez de vous rendre sur votre navigateur préféré, convaincu qu’en entrant les références exactes de la machine, de nombreux sites en ligne vont vous proposer l’achat des pièces à remplacer. Ainsi, lors de votre périple numérique, vous tombez sur des sites au sérieux plus ou moins douteux, qui semblent pouvoir fournir cette fameuse pièce. Pas de photo ni d’élément descriptif, d’autant plus que le prix affiché, même en devise étrangère est étonnamment élevé. Idem pour les délais de livraison, supérieurs à 3 semaines !
En bref, rien n’est fait pour vous rassurer et un ulcère commence à naître à la naissance de votre estomac. A ce stade, même si la pièce de remplacement est onéreuse, c’est toujours mieux qu’avoir des machines en arrêt de production. Il suffit simplement de patienter 3 semaines et de piocher dans les stocks d’ici là. Pensez quand même à téléphoner à Jocelyne du service production, afin de vérifier l’état des stocks.
Parallèlement, le souvenir de la partie de bowling contre l’équipe de Michel de la compta, lors de la dernière soirée du personnel, vous rappelle que c’est un être tenace et rancunier ! Si vous ne souhaitez pas avoir des remarques sur une pièce foireuse achetée trop chère jusqu’à la retraite, mieux vaut quand même prendre quelques précautions.
Ainsi, la décision tombe : il faut chercher une entreprise capable de reproduire une pièce sur mesure, respectant strictement les caractéristiques de la pièce venant de se casser.
Vous trouvez le numéro de 3D SKULT par le plus grand des hasards Google (enfin c’est ce que vous pensez) et cette fois ci, au bout du fil, quelqu’un décroche !
Voyons maintenant en détail la suite de cette formidable aventure.
Etat des lieux, diagnostic et élaboration du cahier des charges
Vous l’aurez compris, même si tout ne s’est pas passé exactement comme illustré dans l’introduction de cet article, cette situation est à ce jour de plus en plus commune.
Le projet décrit ici fait suite à la casse d’un carter de protection d’un robot utilisé dans les chambres de stérilisation d’un hôpital. C’est un système mécatronique, contenant de nombreux éléments électriques, travaillant dans un environnement très contraint : chaleur et humidité. Ainsi, l’absence de carter de protection est une catastrophe pour la préservation de l’intégrité de ses composants électroniques.
Le cas de figure présentement décrit est dû à l’absence totale d’approvisionnement de pièces détachées pour une raison simple : le dépôt de bilan du fabricant de robot.
Qu’en est-il de la pièce détachée en question ?
Il s’agit d’une pièce monobloc, en plastique injecté, matière ABS et de couleur jaune. De forme rectangulaire aux extrémités arrondies, elle accueille deux logements : un pour un bouton de mise sous tension, et l’autre pour un détecteur de positionnement. La fixation est réalisée classiquement, en « sandwich » par vissage direct sur le corps de la machine.
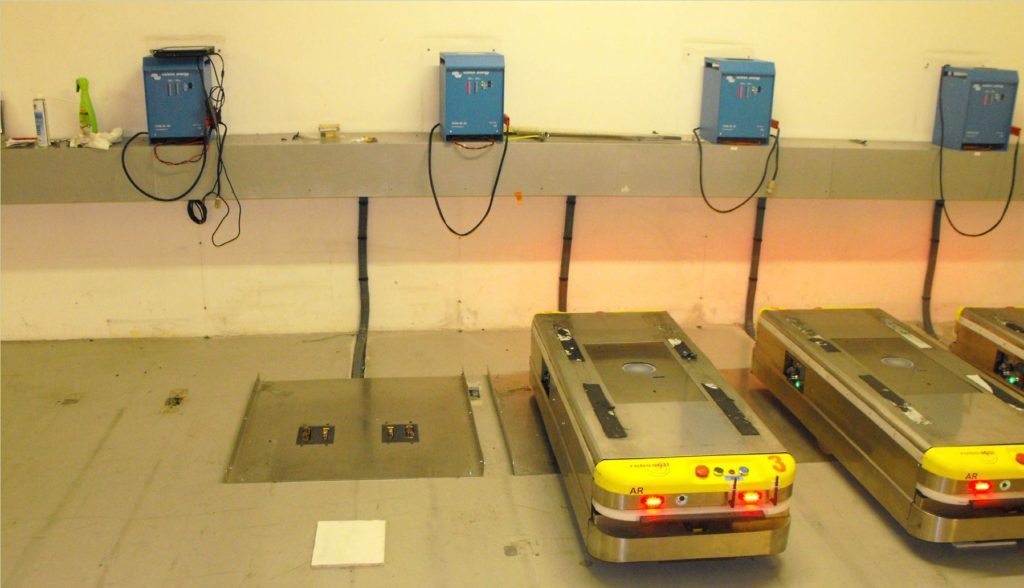
A ce stade, la plus prudente des démarches voudrait que la pièce cassée soit envoyée, pour effectuer un relevé de côte précis dans le but de la re-modéliser. Cette étape porte le doux nom de rétro-conception. Un article sera prochainement dédié à ce vaste domaine !
Démarche prudente, oui mais… !
Il ne faut pas oublier que pendant ce temps, la machine en question est à l’arrêt, perturbant le cycle de fonctionnement de l’unité de stérilisation de l’hôpital. Fort heureusement, le responsable biomédical à l’origine de l’appel possède les plans de la pièce dans ses dossiers de maintenance. Après transmission de ces plans, la modélisation a pu être entamée sans délais.
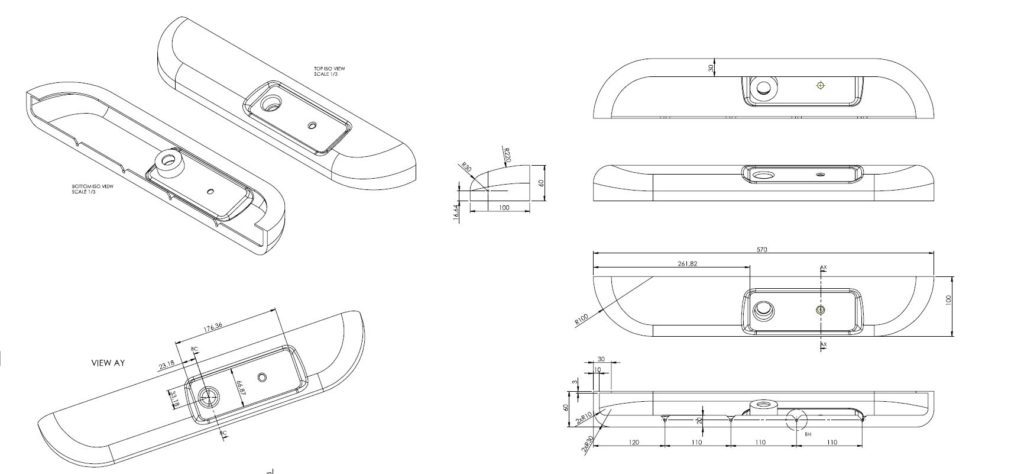
Rétro-conception : chercher l’identique ?
Une fois la modélisation stricto-sensu terminée, celle-ci sert de fondation à la pièce de remplacement à créer. En effet, remplacer à l’identique dans le cas de pièces d’usure ou de consommables paraît tout à fait cohérent. Dans le cas présent, la casse de cette pièce ne semble pas faire partie d’un cycle d’utilisation et/ou de maintenance normal.
Après concertation avec le donneur d’ordres il a été décidé d’établir une amélioration de la pièce : c’est la phase de rétro-ingénierie.
Rétro-ingénierie : quel intérêt, d’autres ont déjà réfléchi !
Depuis la nuit des temps, l’ingénierie est basée sur une approche mêlant théorie, pragmatisme et empirisme. L’optimisation de ces trois composantes reflète la conception idéale. Généralement toute conception joue de manière différente, agitant les curseurs d’une certaine manière pour obtenir un équilibre acceptable.
Sans rentrer dans une analyse complète et rébarbative des solutions techniques initialement choisies par le constructeur, il est évident que l’équilibre de la conception de cette pièce repose sur une béquille. A chacun sa propre interprétation pour la placer sous une des trois composantes citées précédemment.
Ainsi, la faiblesse apparente de cette conception est avant tout la robustesse. En effet, s’agissant d’une machine autoguidée, il est facilement compréhensible que des situations de choc sont souvent rencontrées. Le choix d’un carter monobloc est donc à contester car non seulement il inflige une propagation de contrainte à l’ensemble de la pièce lors d’un choc, mais impose aussi le remplacement de l’entièreté de la pièce lors d’une casse. Enfin, le choix du matériau est aussi à remettre en cause. En effet, une pièce plastique monobloc, corrélée aux contraintes de chaleur et d’humidité fait qu’inexorablement, des usures et/ou modifications structurelles sont à anticiper.
Solutions techniques proposées, choix des matériaux et procédés
Après avoir fait bouillir nos méninges, trois modifications de conception ont été établies.
Améliorer la résistance, quoi qu’il en coûte !
Etant donné que l’hôpital dispose de plusieurs machines, le pari que d’autres protection vont casser de la même manière ne semble pas si hasardeux.
Dans un premier temps, le changement fondamental opéré concerne le passage d’une pièce monobloc à une pièce multi-composants.
Le fait d’associer plusieurs unités indépendantes permet d’atteindre deux améliorations majeures : augmentation de la résistance mécanique en créant des zones de fuite de contrainte aux joints d’assemblage d’une part ; et possibilité de maintenance ou remplacement minimisée. En effet, si un seul composant est cassé, inutile de remplacer l’ensemble !
Nous venons donc de pousser à fond le curseur du pragmatisme n’est-ce pas ?
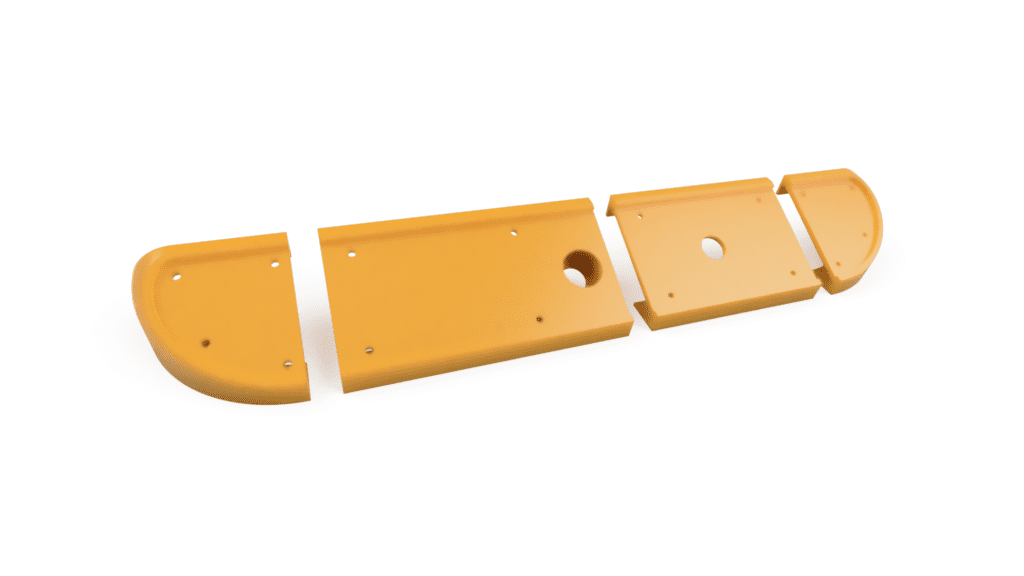
Renforcer l’homogénéité et « pimper » l’apparence
Le multi composant c’est bien. Pour autant, afin que la résistance soit maximale, il faut un liant, un socle commun.
Le choix s’est porté sur une pièce métallique commune assurant rigidité et homogénéité. Ainsi, les multi composants plastiques, au nombre de quatre, sont solidarisés par une plaque, assurant rigidité et planéité.
Au sein de cette plaque, les réservations sont laissées afin de pouvoir intégrer les éléments électroniques extérieurs : bouton de mise en route et détecteur d’obstacles. Leur emplacement a également été revu, afin de mieux correspondre aux cas d’utilisation décrits par le donneur d’ordre. Le retour d’expérience au service de l’utilisateur !

Et les matériaux utilisés ?
Concernant les quatre composants plastiques, l’ABS a été conservé. Les pièces sont fabriquées en impression 3D FDM (dépôt de filament). Résistant aux chocs et tolérant à la chaleur, il reste un candidat idéal. Cependant les épaisseurs de matière ont été augmentées et l’adjonction de la plaque métallique permettent de réduire l’inertie de la matière vis-à-vis du vieillissement et des contraintes de son environnement d’utilisation.
La plaque métallique, est en acier inoxydable 304L de grade médical. Ses propriétés de résistance à la corrosion et aux solvants sont parfaitement adaptées à l’utilisation dans le domaine médical, et sa rigidité augmentera de façon drastique l’homogénéité de l’ensemble et donc la résistance. La plaque sera découpée au laser.
Ainsi, par ces quelques modifications, un système plus efficace a été créé : souplesse vis-à-vis de la contrainte fuyante au niveau des plans de joint, et résistance conférée par l’ajout d’une plaque métallique.
Prototypage, test et fabrication série
Dans un premier temps, une unité a été fabriquée puis envoyée de manière à tester et ainsi valider le nouveau design.
Après validation, une série de 10 exemplaires a été lancée, remplaçant l’intégralité des carters du parc machine.
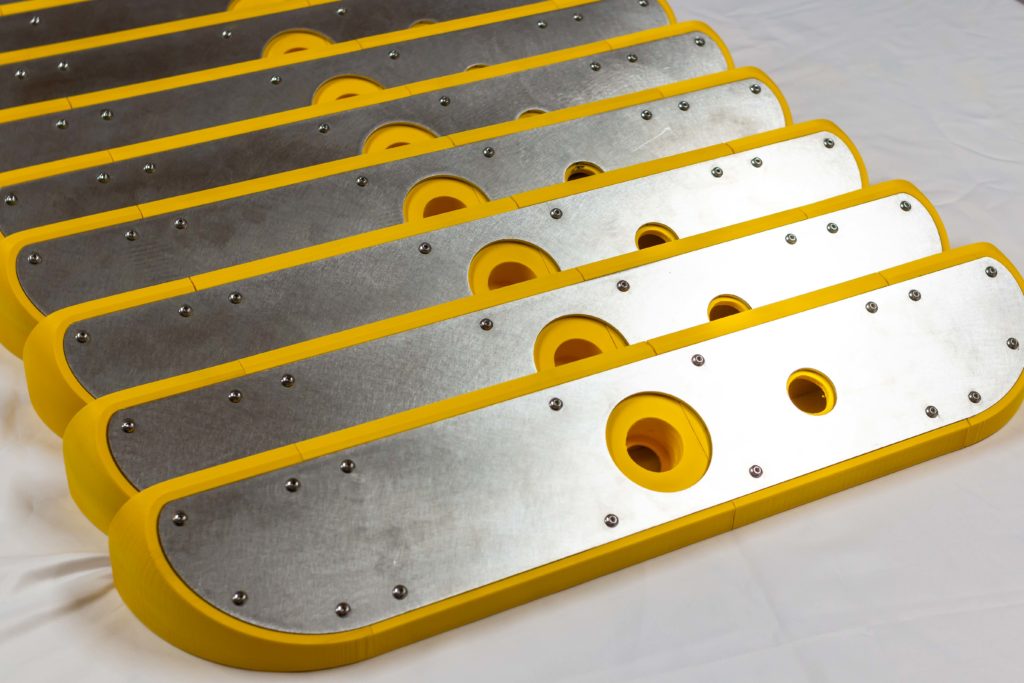
Finalement, entre la prise de contact et la réception du prototype, 2 semaines se sont écoulées, permettant de remettre en service le robot défaillant sous un délai raisonnable. Les 9 autres unités ont été livrées 3 semaines après, soit 5 semaines après le premier appel et 3 semaines après validation du prototype.
Ainsi, d’une pièce cassée un beau matin, sans perspective ni solution évidente de remplacement, nous avons pu proposer et fournir une pièce reconçue et donc améliorée, dans un court délai, et avec assurance de réussite grâce au test d’un prototype avant de fabriquer une série complète.
Théorie, pragmatisme et empirisme : le tryptique idéal pour un succès garanti !
Il est maintenant 10H30. Si vous venez de constater qu’une de vos machines est en panne et que vous n’avez pas de solution évidente de remplacement, ne ratez pas la prochaine pause-café et contactez-nous directement !